About US
From Jerng Sing to Yang-Bo, our experience has expanded from the domestic market to the global stage. Over the past 23 years, Yang-Bo has seen tremendous growth, enhancing our facilities and providing comprehensive services to our customers
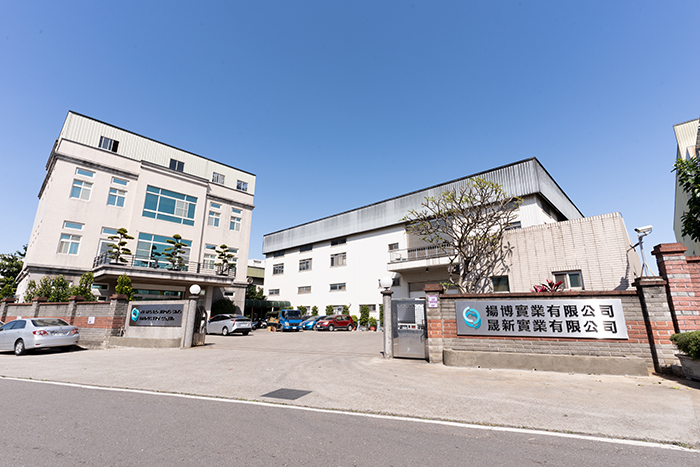
Company Important Things
- Passed ISO9001: 2000 certification in 2001
- Passed SGS ISO22000 HACCP certification in 2012
- Passed SGS ISO/TS22002-4 certification in 2014
- Passed ISO FFCS certification in 2018
- Passed the air pollution permit approved by the Environmental Protection Agency in 2019
Our printing machines and quality inspection equipment are equipped with CCD technology, featuring computerized automatic detection that identifies printing abnormalities and issues warnings to ensure the highest product quality
Production Process
Step 1 Require From Quotation (RFQ)
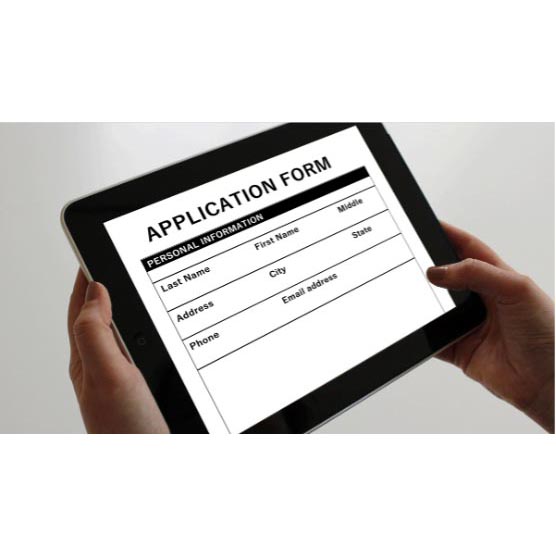
Fill up the form or send your requirements to our email :
Step 2 Confirms And Reviews The Design With Our Customers
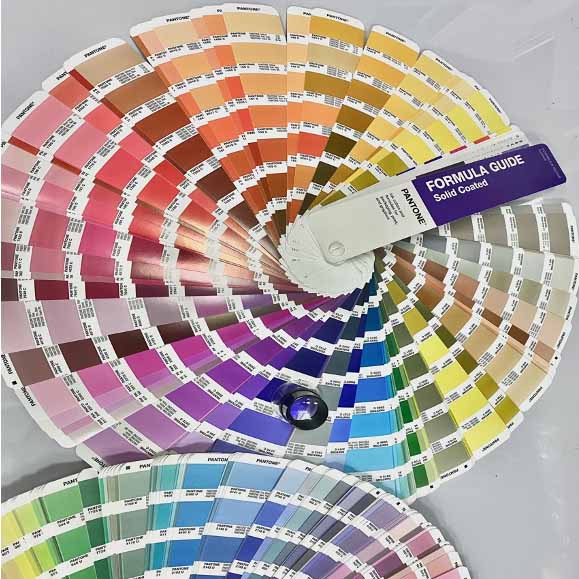
The customer emails the artwork, which is confirmed by our art designer before making the cylinder plate
Step 3 Verify The Cylinder Plate Before Mass Production
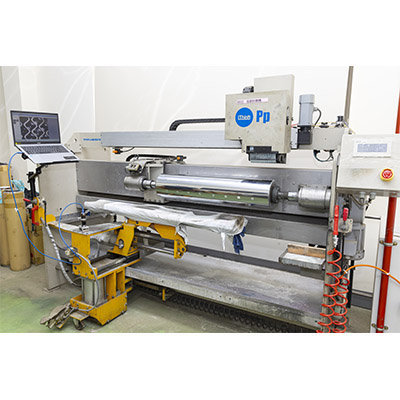
After the plate making is completed, check and grind the plate before printing on the machine (to reduce the NG rate).
Step 4 Print
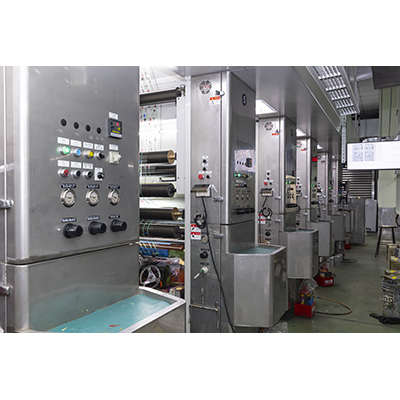
In gravure printing, ink is applied to a cylinder plate, the excess is removed, and the remaining ink in recessed areas is transferred to the printing material under high pressure to imprint graphics and text
Step 5 Quality Inspection
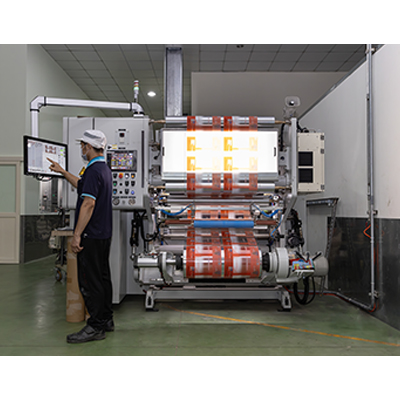
The final printed product undergoes a quality check using a machine equipped with CCD to identify and remove any defective prints, ensuring high-quality output.
Step 6 Lamination
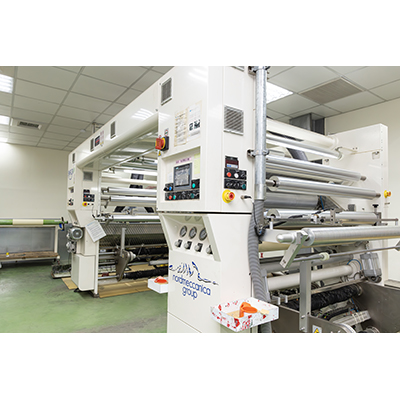
A high-speed dry laminating machine evenly applies adhesive across the non-heat sealable film.
Step 7 Slitting
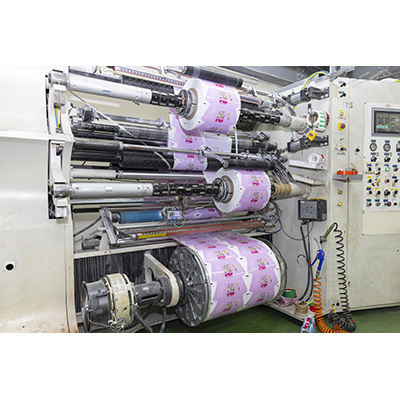
Featuring advanced tension control and infrared edge alignment systems, the equipment can precisely cut materials to the customer's specified dimensions.
Step 8 Dividing
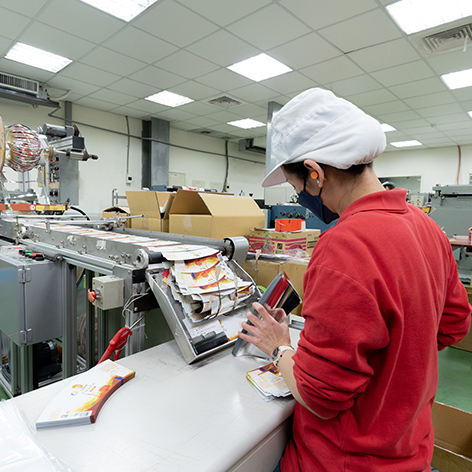
This production method is the unique final step for IML. Each sheet is individually pressed and cut to guarantee uniformity in size for every finished product without discrepancies.
Step 9 Stamping
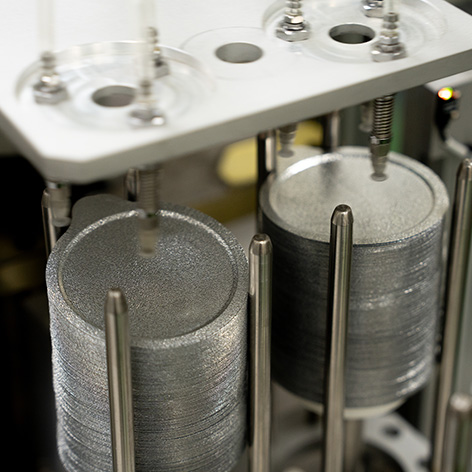
Aluminum foil sealing film is produced using multi-mode stamping, cutting, and automatic stacking to ensure uniform sizing and error-free finished products.
Step 10 Inspection Of Finished Products Before Shipment
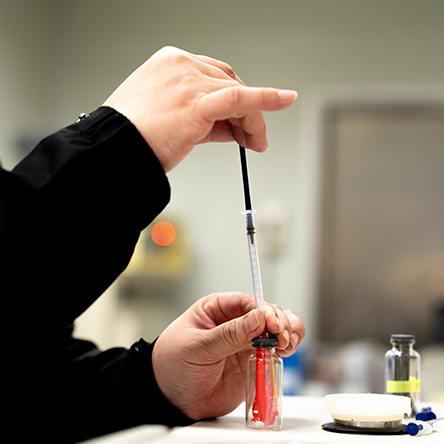
Quality control utilizes specialized laboratory equipment to perform random inspections based on customer-specific data.